25 April 2022
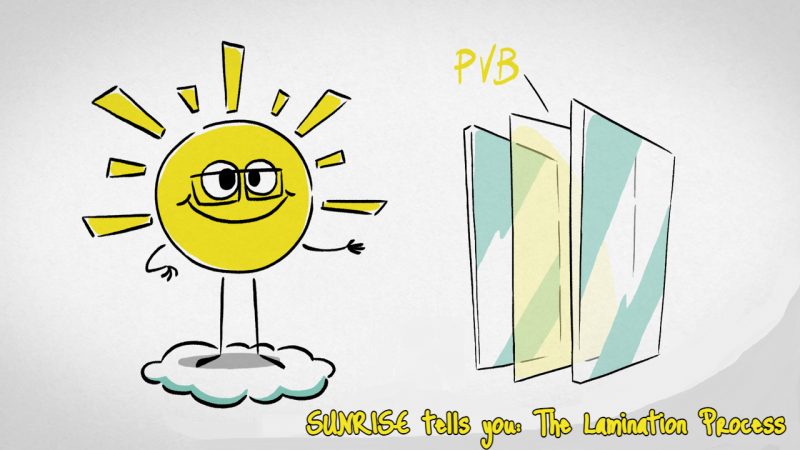
Laminated glass is usually the composition of two or more sheets of glass, joined together with one or more interlayers of thermoplastic material (PVB), by a hot and pressure process.
PVB acts as an adhesive and separator between the glass sheets, changing their mechanical, thermal and acoustic performance.
The sheets of glass to be laminated that feed the production line are first washed and dried, to eliminate the risk of low adhesion and delamination localized in the finished product. Then, in an air-conditioned environment, the sheets of PVB are laid between the glass sheets, depending on the type of product desired, by means of an automatic bridge. The surplus of PVB compared to the final size of the sheet is then removed with automatic cutting machines.
The assembled multilayer sheet then passes into a first heating furnace, where it is preheated to 30 ºC and calendared to facilitate the deaeration process, eliminating almost all the air present between the PVB and the glass sheets.
In a second heating furnace the temperature rises to 60 ºC, to complete the process of deaeration and activate the adhesive properties of the PVB. During this phase, the multilayer sheet passes under other machines, which complete the sealing at the edges and prevent the entry of air before self-cleaning (a visual examination is carried out to evaluate the success of the process). The phases of an autoclave cycle are pressurization, heating, maintenance, cooling, and depressurization. At the end of the cycle, laminated glass has completed the production process and is subjected to quality controls, to determine compliance with current regulatory requirements.
Then it is packed and poured into stock, ready to be sold.
Leave A Comment